Comprehensive Rail Inspection and Monitoring: Enhancing Safety and Efficiency through Risk-Based Engineering
The safety of railway operations across the globe relies significantly on the quality and integrity of the railway tracks. Tracks in good condition serve as the foundation for safe and reliable transportation, reducing the likelihood of accidents and ensuring smooth operations. Achieving and maintaining such safety standards in the most efficient and cost-effective manner involves the implementation of Risk-Based Engineering principles. These principles provide a structured framework for assessing and mitigating potential risks associated with railway tracks.
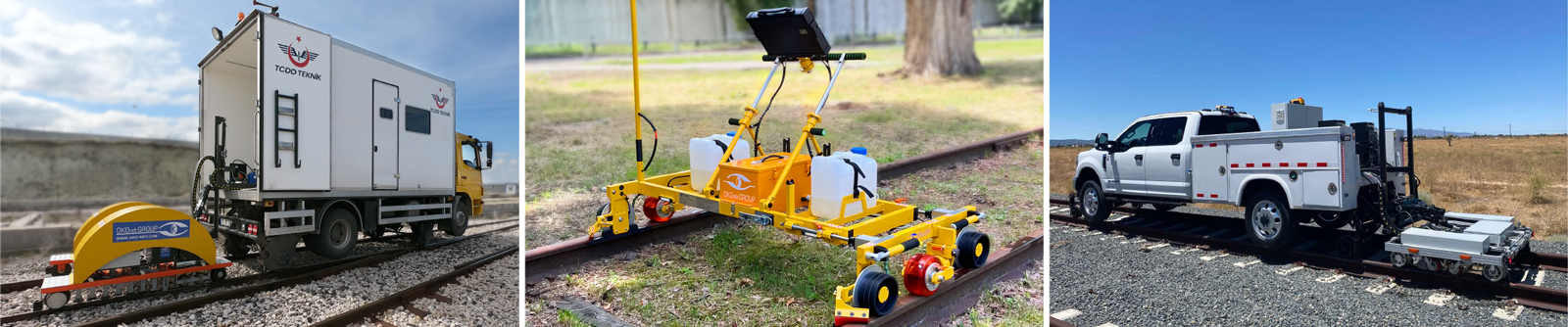
At the core of the Risk-Based Engineering approach is Risk Assessment, a systematic process designed to identify, evaluate, and address potential hazards. This process begins with a detailed Potential Failure Mode Analysis (PFMA), which involves identifying possible ways in which the railway track could fail and determining the underlying causes, or Initiators, for each failure mode. Among these Initiators, fatigue damage emerges as one of the most widespread and critical categories. Fatigue damage refers to the gradual deterioration of rail material due to repeated stress over time, which, if left unchecked, can lead to severe failures.
Effectively managing and mitigating the risks associated with fatigue damage requires comprehensive and up-to-date information about the condition of every rail across the railway network. The ability to accurately identify and monitor defects in rails is crucial, as it enables railway operators to carry out timely interventions, such as replacing or repairing defective sections. This proactive approach prevents the progression of failures and ensures the continued safety and reliability of railway operations.
One of the most effective methods for detecting defects in railway tracks is ultrasonic rail inspection. This advanced technology utilizes high-frequency sound waves to identify both surface-level and internal flaws within the rail material. Ultrasonic inspection is capable of examining the entire cross-section of the rail, with the exception of the rail base wings, and can detect both surface and internal defects. Typically, ultrasonic rail inspections are carried out in three distinct stages:
High-speed rail inspection
This stage involves the use of specialized equipment, such as hi-rail vehicles, motorized railcars, and standard railway cars, to perform rapid inspections over extensive track sections. This method ensures the quick identification of critical defects while covering significant distances efficiently. The data collected during high-speed inspections is transmitted to regional ultrasonic testing (UT) inspectors for further analysis and confirmation of any suspicious indications. Once validated, the information is uploaded to a centralized Railway Infrastructure database, ensuring that accurate and current data about the technical state of every segment of the railway track is readily available.
Inspection using hand-pushed flaw detectors
For more localized and detailed inspections, hand-pushed single-rail and dual-rail flaw detectors are employed. These devices are particularly useful for confirming defects identified during high-speed inspections and for routine examinations of areas with complex track layouts, such as sections with low radius curves, multiple switches, and other challenging features. The data obtained from hand-pushed detectors is comparable in format to that from high-speed systems, allowing for seamless integration into the centralized database and facilitating comprehensive analysis.
Detailed manual inspection
In cases where further investigation is required, detailed manual inspections are conducted using handheld flaw detectors. This stage provides in-depth analysis of specific defects identified in previous stages. Manual ultrasonic testing is also employed for acceptance and maintenance testing of aluminothermic rail welds, ensuring their durability and safety.
The integration of all three levels of ultrasonic testing—high-speed inspection, hand-pushed detector inspection, and manual flaw detection—creates a comprehensive and robust rail quality monitoring system. This multi-layered approach not only enhances the safety of railway operations but also significantly improves the cost-effectiveness of track maintenance by enabling timely and precise interventions. By leveraging advanced inspection technologies and maintaining a centralized database of rails condition, railway operators can ensure the long-term reliability and efficiency of their infrastructure. The products of OKOndt Group enable the implementation of each described stage of comprehensive inspection, ensuring maximum reliability and efficiency.