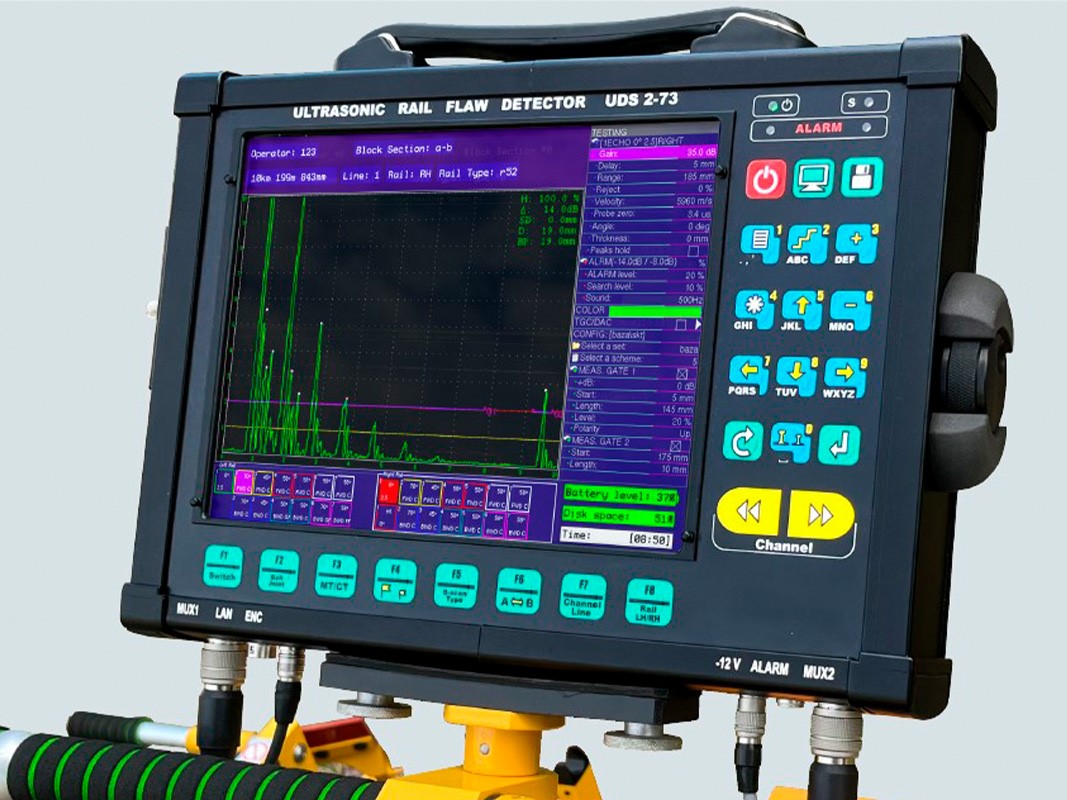
Hand-pushed flaw detectors, such as the UDS2-73 and UDS2-77, are used for confirmatory inspections following high-speed ultrasonic rail testing or for primary inspections of small track sections, tight-radius curves, station tracks, and other areas where high-speed systems are impractical or ineffective.