Since early 2010, the OKOndt Group company has been conducting scientific-and-research and experimental-and-design works in the field of automation of the non-destructive testing methods for the railway wheelset elements testing. Implementation of the developed Systems for automated ultrasonic testing AUTS Axle-4 OS-4 and mechanized magnetic particle testing OS-38 (hereinafter – the Systems) enabled the enterprises of PJSC «INTERPIPE NTRP» and PJSC Lugcentrokuz a. S. Monyatovsky to promote their product at the world market and successfully certify their quality labs for compliance with requirements of European and American regulatory documents.
Automation of inspection allowed the Customer to bring the quality of the manufactured products to zero-reclamation level, as well as to strengthen their renommée of the manufacturer of flawless goods.
After carrying out an industrial operation and obtaining its positive results at PJSC “INTERPIPE NTRP” and PJSC Lugcentrokuz a. S. Monyatovsky enterprises, the company DDAP-RAX LLC purchased the OS-38 and AUTS Axle-4 OS-4 Systems in 2021. In February 2022, the System OS-38 passed industrial tests at the Customer’s site and ensured the company’s successful compliance as a railway axles manufacturer during the international audit, thus opening the gateway for their products to the Northamerican and European markets.
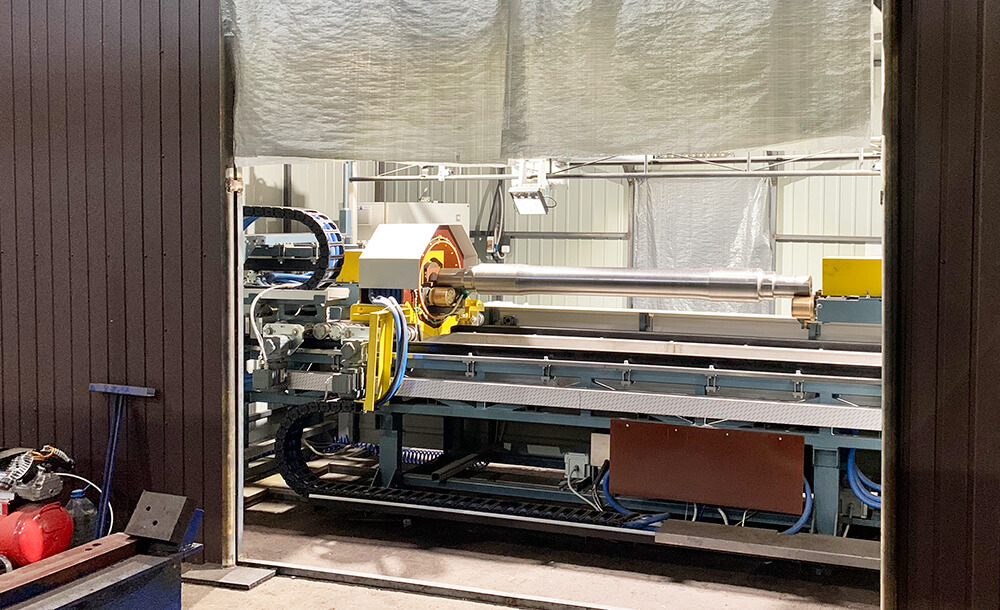
Figure 1 – Appearance of the OS-38 System
The System provides inspection of the axles for compliance with the following regulatory documentation:
- AAR M101 — Manual of Standards and Recommended Practices Whels and Axles. Axles, Carbon steel, Heat-Thread.
- EN 13261 — Railway applications — Wheelsets and bogies — Axle — Product requirements.
The System OS-38 enables testing of various dimensions (by length, diameter), and the flexibility of its design allows to modify the System to any Customer’s assortment. The System can be built in two versions:
- upper axles loading (by means of a Customer’s equipment)
- equipped with the storage and loading rack of the lateral loading (high-output version, up to 24 axles/hour).
The System provides for the surface defects detection of longitudinal and transverse orientation (relative sensitivity corresponds to the level «B» as per GOST 21105) in correspondence with EN 13261, AAR M101, by wet fluorescent magnetic particle method, by combined way of magnetization (circular, longitudinal) with alternating current (АС) application. OS-38 ensures 100 % testing of the whole axle’s surface, except for the buttends.
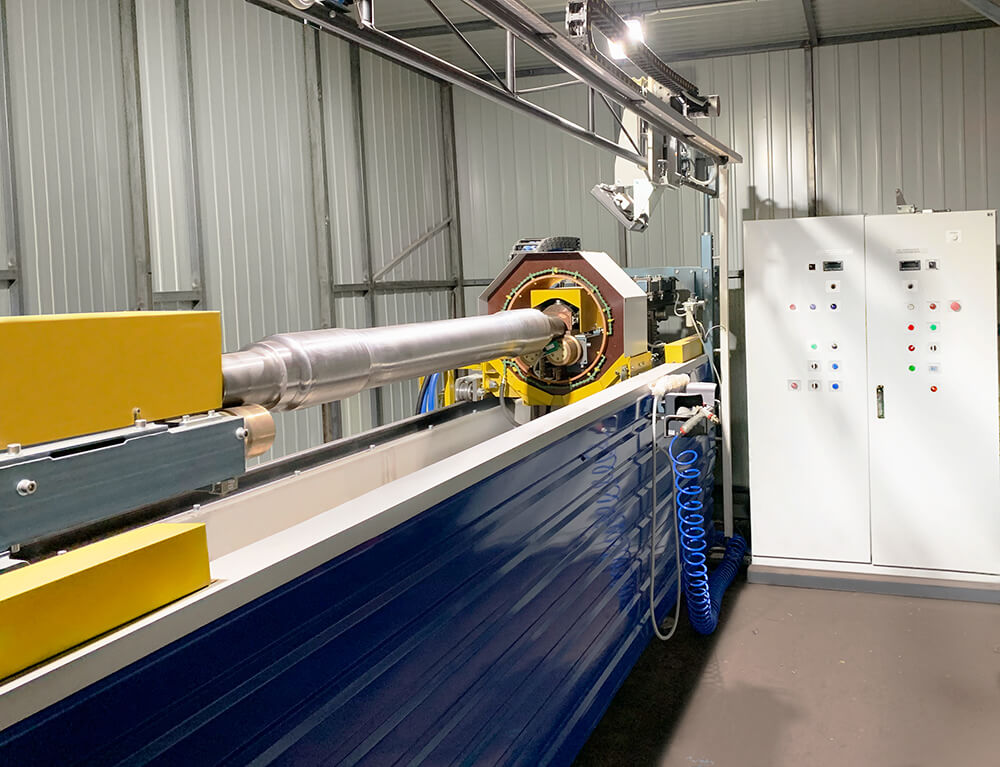
Figure 2 – Operator’s work place of the OS-38 System
The testing is carried out by the way of attachment in a rotating magnetic field (automated and manual) with the use of high-intensive UV irradiators.
The process of testing is completely automated. When the axle is loaded, the conditions preset by the Operator for the testing are set automatically and controlled by the automation mechanism during the entire test cycle. Application of the magnetic indicator, setting and monitoring of the magnetizing currents, axle rotation, UV irradiator movement, demagnetization are performed automatically by the Operator’s command. During visual examination and taking a decision the Operator can adjust the axle rotation or UV irradiator movement speed, make another magnetization or apply additional magnetic indicator using the Operator’s control panel. Closed-loop application of the magnetic indicator minimizes the consumption of magnetic indicators. Application of an innovative barbotage system allows to get a high-quality magnetic particles suspension in a carriage.
Specifications short list:
- Allowable maximum diameter of the tested axles: up to 390 mm*
- Maximum length of the tested axles: 2600 mm*;
- Possibility of a testing video recording in automatic mode
- Output:
- 10 axles/hour – in the System version with upper loading by Customer’s equipment
- 24 axles/hour – in the version with storage and loading rack of the lateral loading.
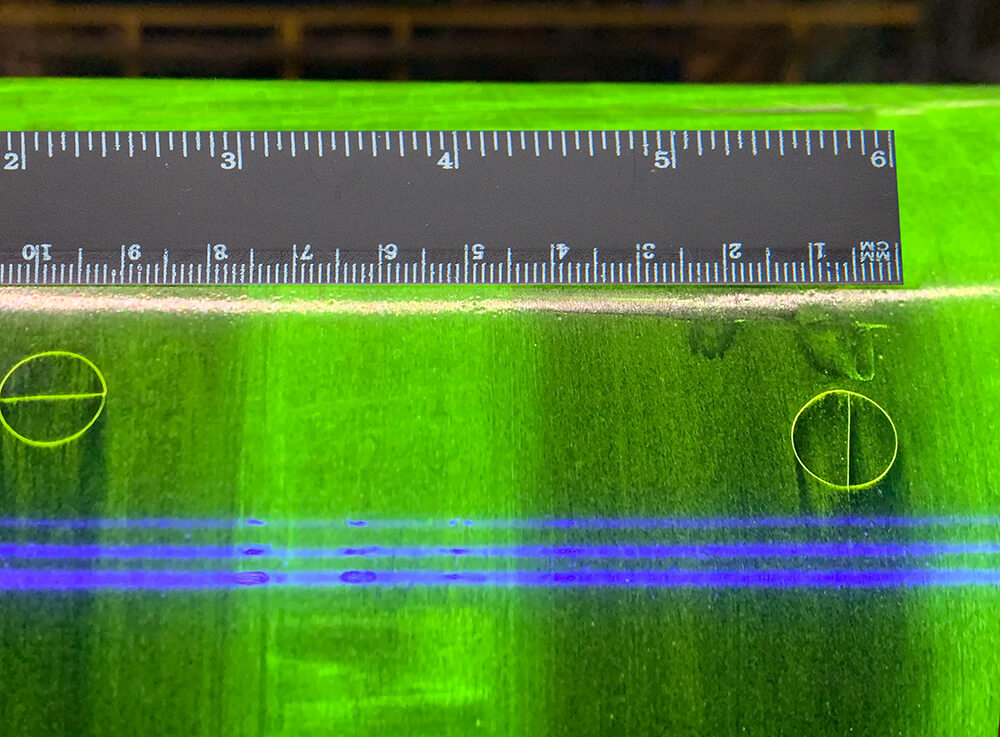
Figure 3 – Appearance of indications of transverse, longitudinal, and multidirectional discontinuities revealed in the process of industrial testing using the reference standards of a Customer
*- the System can be adjusted to other axle parameters upon the Customer’s request
The System includes a welded bearing frame with an axis rotation system, an automatic system for moving the rotation rollers to fit the axle size, a stainless steel waste suspension collection tank, and a system for mechanized movement of the UV irradiator.
OS-38 System’s advantages
- The System allows to perform testing of axles with various profiles (including tram axles).
- The System provides both fluorescent and classic color wet magnetic particle testing.
- The automated barbotage system increases lifespan of the magnetic indicator as well as the quality of particles application onto the tested object.
- current-transmitting wear-resistant contacts of circular magnetization allow to test axles both with machined and semi-finished buttend without damaging it.
- The System can be inbuilt in any railway axles production line or be used at any repair shops (enterprises).
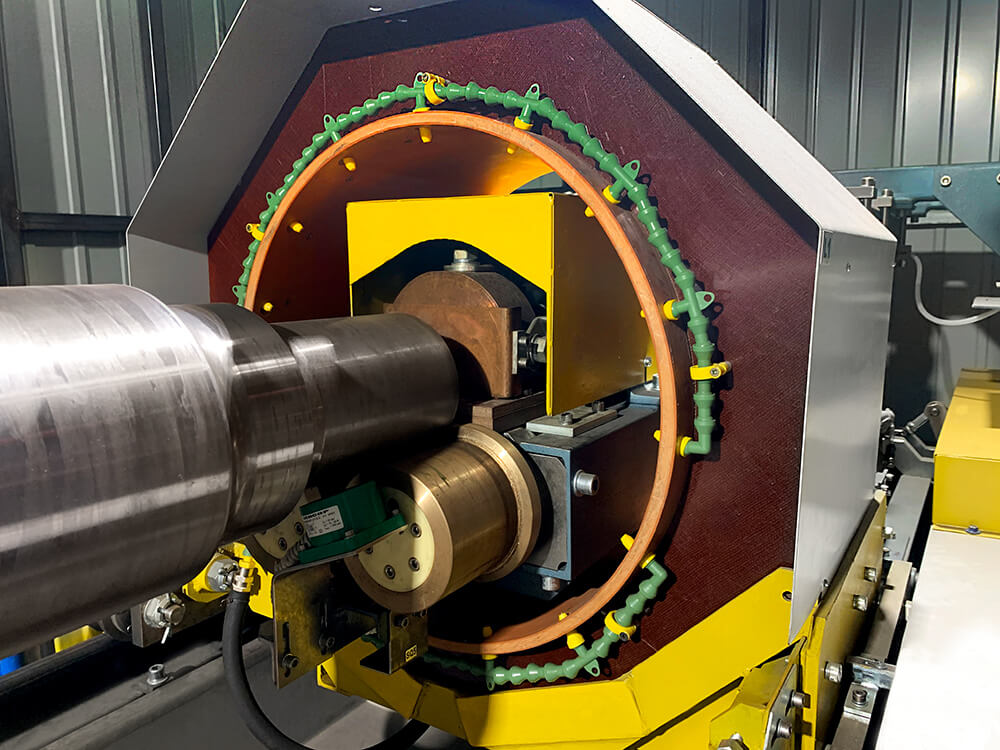
Figure 4 –The circular and longitudinal magnetization units, magnetic indicator application (magnetic suspension), axle rotators, UV irradiator
Implementation:
- First ОS-38 System was implemented at PJSC “INTERPIPE NTRP” in 2015. Use of the System enabled the enterprise to ensure a high quality of their products and almost completely bring customer complaints to zero. PJSC “INTERPIPE NTRP” exports their goods to many countries of Europe, Asia, North and South America, Africa.
- Second ОS-38 System passed industrial tests and has been implemented in the production process at the DDAP-RAX enterprise which is one of the leaders in railway axles production in February 2022. Implementation of the System enabled the company to increase the quality of their products, certify them in compliance with the foreign markets, so to strengthen their export potential.
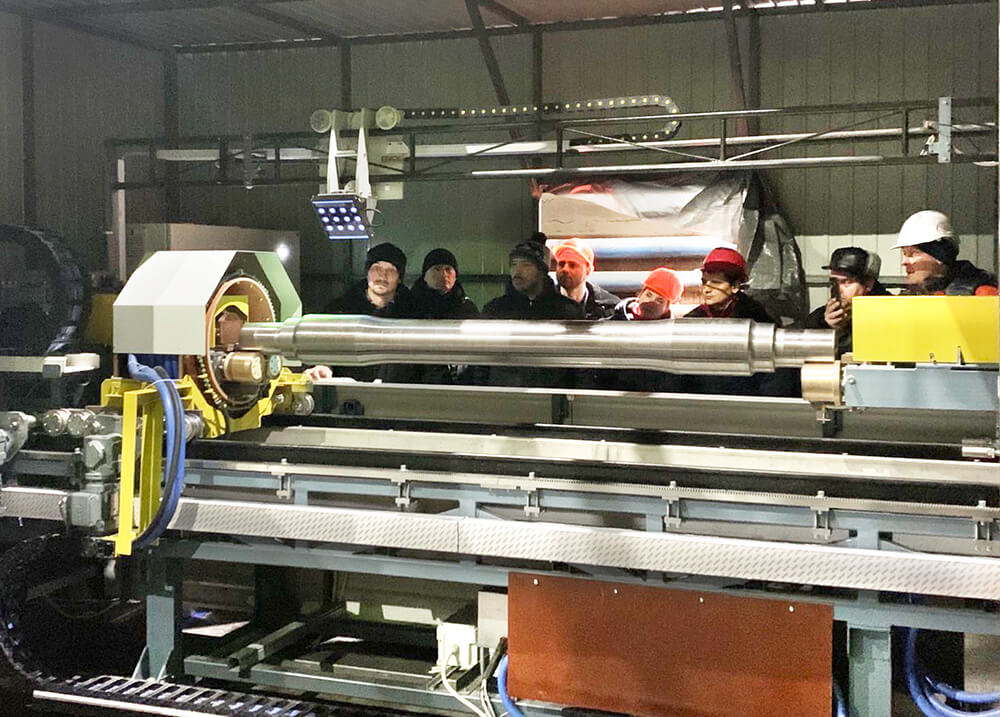
Figure 5 – Finishing the industrial tests with participation of the Customer’s commission members and the Developer’s experts
We’d like to emphasize that the DDAP-RAX company also purchased the System for ultrasonic immersion testing of the axles OS-4 (AXLE-4).