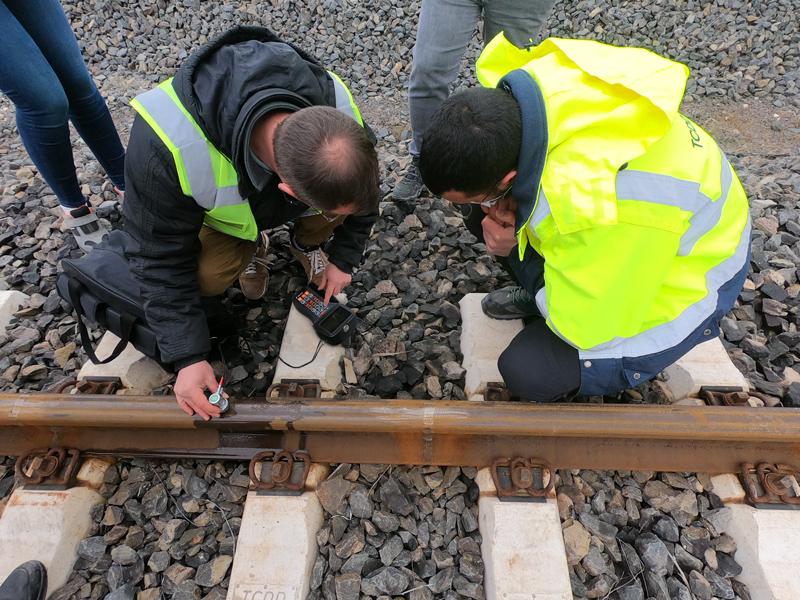
La inspección manual de carriles en la vía férrea se utiliza en dos casos:
- Para la inspección de confirmación de los defectos detectados durante la inspección continua de carriles con detectores de fallas de uno o dos carriles o, en algunos casos, con sistemas de inspección de carriles por ultrasonidos de alta velocidad.
- Para la inspección de aceptación de juntas de soldaduras aluminotérmicas de rieles.